PD340 - Batch Control
- with PD 340 Flow Transmitter and PD 210 Display
The PD 340 Flow Transmitter has a built-in batch control function, and can therefore easily be used to control the dosing of a specified volume. The requested volume is keyed into “SETPOINT” on the PD 210.
– Input 1 on PD 340 is used to start the batch control.
– Output 2 controls the dosing valve or pump.
The Volume 2 counter shows the dosed volume.
When the batch control function is used, the built-in flow regulator cannot be used.
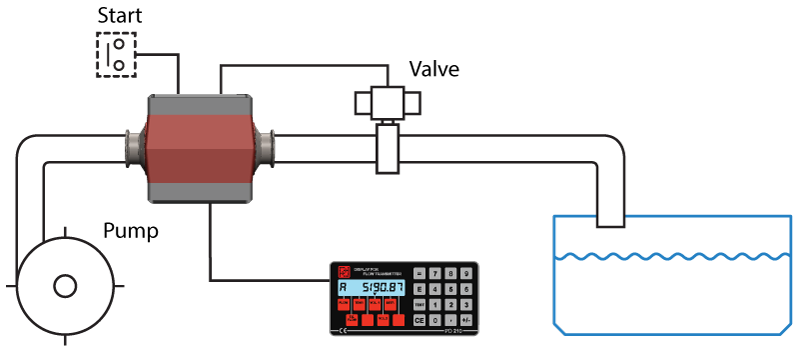
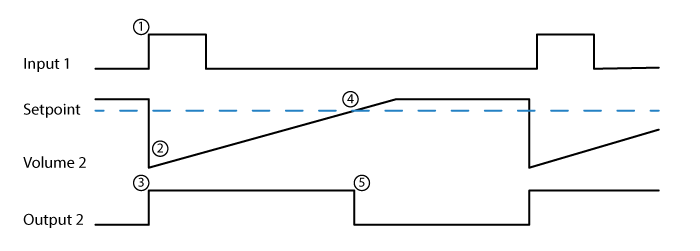
The function of the system
At first the requested volume is keyed into “SETPOINT”.
The dosing will start when input 1 is activated.
This will clear the Volume 2 counter and Output 2 goes on. The valve or pump controlling the flow must be activated by the relay. When the liquid starts to flow, “Volume 2” will count up and when it is equal to the setpoint, Output 2 will switch off.
Because of the reaction time of the valve or pump, the flow will not stop immediately after Output 2 is switched off. Consequently the actual dosed volume is a little higher than the setpoint.
This after-flow is fairly constant if the reaction time and the flow rate are constant, and therefore it is possible to compensate for that by reducing the setpoint with the volume of the after-flow.
The volume of this after-flow can be calculated as [Volume 2 – Setpoint].
Programming the Batch Control
To obtain the requested functions the PD 340 must be programmed as shown next to.
When programming the Flow Transmitter the Program Enable Switch on the terminal board must be in position ON.
Digits marked with * are not used for the batch control function, but should be programmed according to meter size and other working conditions. The manual describes the programming procedure.
When programming is done, the Program Enable Switch should be put back to position OFF.
The value in setpoint register before the program enable switch was switched off will be used as a power-up value after a power-cut.
Programming the registers (w. the PD 210)
E1: | * | * | * | * | * | * |
E2: | * | * | * | * | * | * |
E3: | 0 | 0 | 0 | 0 | 0 | 0 |
E4: | * | * | * | * | * | * |
E5: | * | * | * | * | * | * |
E6: | * | * | * | * | * | * |
E7: | * | * | 2 | 1 | 0 | 6 |
E8: | 3 | 0 | 2 | 4 | * | * |
Electrical Connections in the Terminal Box
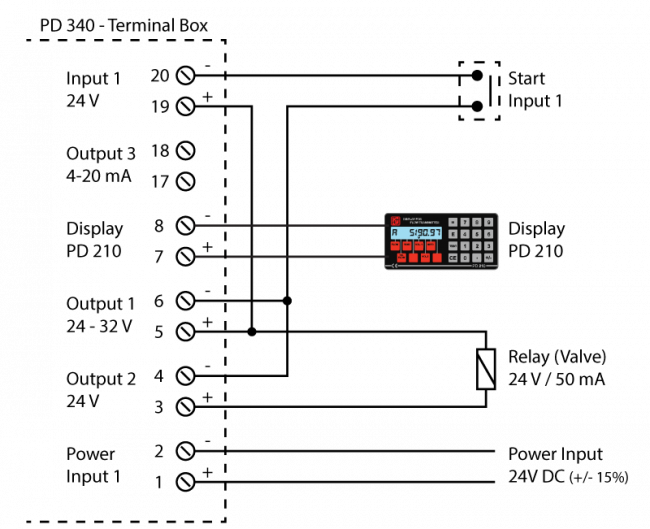
PD340 - Flow Control
- with PD 340 Flow Transmitter and PD 210 Display
A centrifugal pump, a PD 340 Flow Transmitter, and a modulating valve with an I/P converter will form an accurate FLOW CONTROL SYSTEM. Such a system is more accurate, and normally also less expensive than systems using a positive pump with variable speed.
The PD 340 flow transmitter has a built-in PI-REGULATOR which can be operated in AUTO as well as in MANUAL. Input 1 is used for this manual/auto selection.
The requested flow rate is keyed into SETPOINT on the connected PD 210 display.
The output value can be read in % by pressing the untitled key to the left of VOL.2.
If the regulator is in MANUAL, the operator can key the requested output position into the same register.
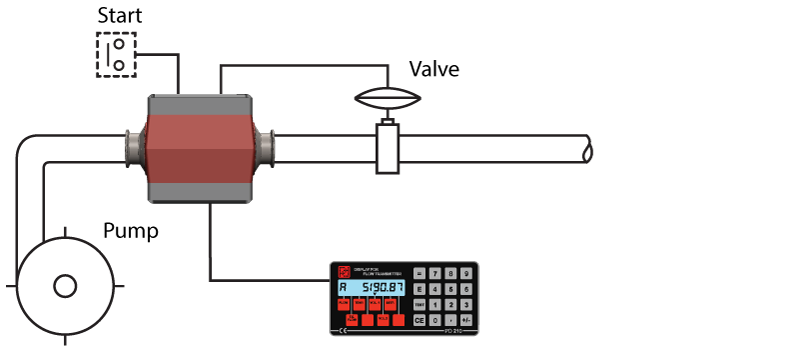
Programming the Flow Control
To enable the PI REGULATOR function in the PD 340, the flow transmitter should be programmed in the following way:
The * indicates that these digits are not in use for this function but should be programmed according to the meter size and other working conditions of the flow transmitter.
The program enable switch must be in position ON during programming.
Programming the registers (w. the PD 210)
E1: | * | * | * | * | * | * |
E2: | T | T | T | T | T | T |
E3: | 0 | 0 | 0 | 0 | A | B |
E4: | * | * | * | * | * | * |
E5: | P | P | P | P | P | P |
E6: | * | * | * | * | * | * |
E7: | 1 | 8 | * | * | 0 | * |
E8: | * | * | * | * | * | * |
T = Ti
P = P-band
The function of the system
The P-band indicates the proportional sensitivity in the same flow units as the “FLOW” register (l/h or gallons/min.). The P-band is equal to the change in flow rate which will change the output from 0 to 100%.
A typical setting of E5 is 25% of maximum flow.
The Ti is the regulators integration time in seconds. Ti is equal to the time the integrating part of the regulator requires to provide the same change on the output as the proportional part for a step in flow rate.
A typical Ti time is 2 sec. The P-band and the Ti can be optimized the experimental way, or by following the rules from the specialized literature.
There are two types of valves. The digit A is set equal to 0 if the valve is normally closed at 4 mA, or set equal to 2 if the valve is normally open at 4 mA.
Digit B in E3 determines the function of the AUTO/MAN. B = 0: The regulator is always in auto. B = 2: If input 1 is on, the regulator is in MANUAL, otherwise in AUTO.
The P-band, Ti and Setpoint can always be changed because these registers are stored in RAM. The contents will disappear after a power-cut, unless the programme enable switch is in position ON. In this case the contents of P-band, Ti and SETPOINT are stored in EEPROM, and restored in RAM after power-up.
The program enable switch must be switched off after the programming to preserve the EEPROM memory.
Valve size
It is very important to select the correct valve size. Which size to choose depends on the following information:
The minimum and maximum flow rates, the flow/pressure curves of the pump, and the pressure drop in the pipework at the specified flow rate. It is normally recommendable to let the supplier of the modulating valve select the size.
Electrical Connections in the Terminal Box
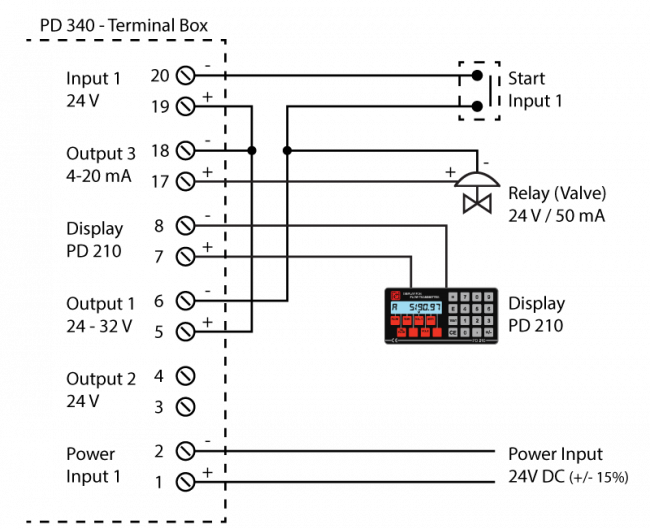